3 min read
The year 2022 for industrial robots: trends in automation
fruitcore robotics
:
Dec 30, 2022 8:29:00 AM
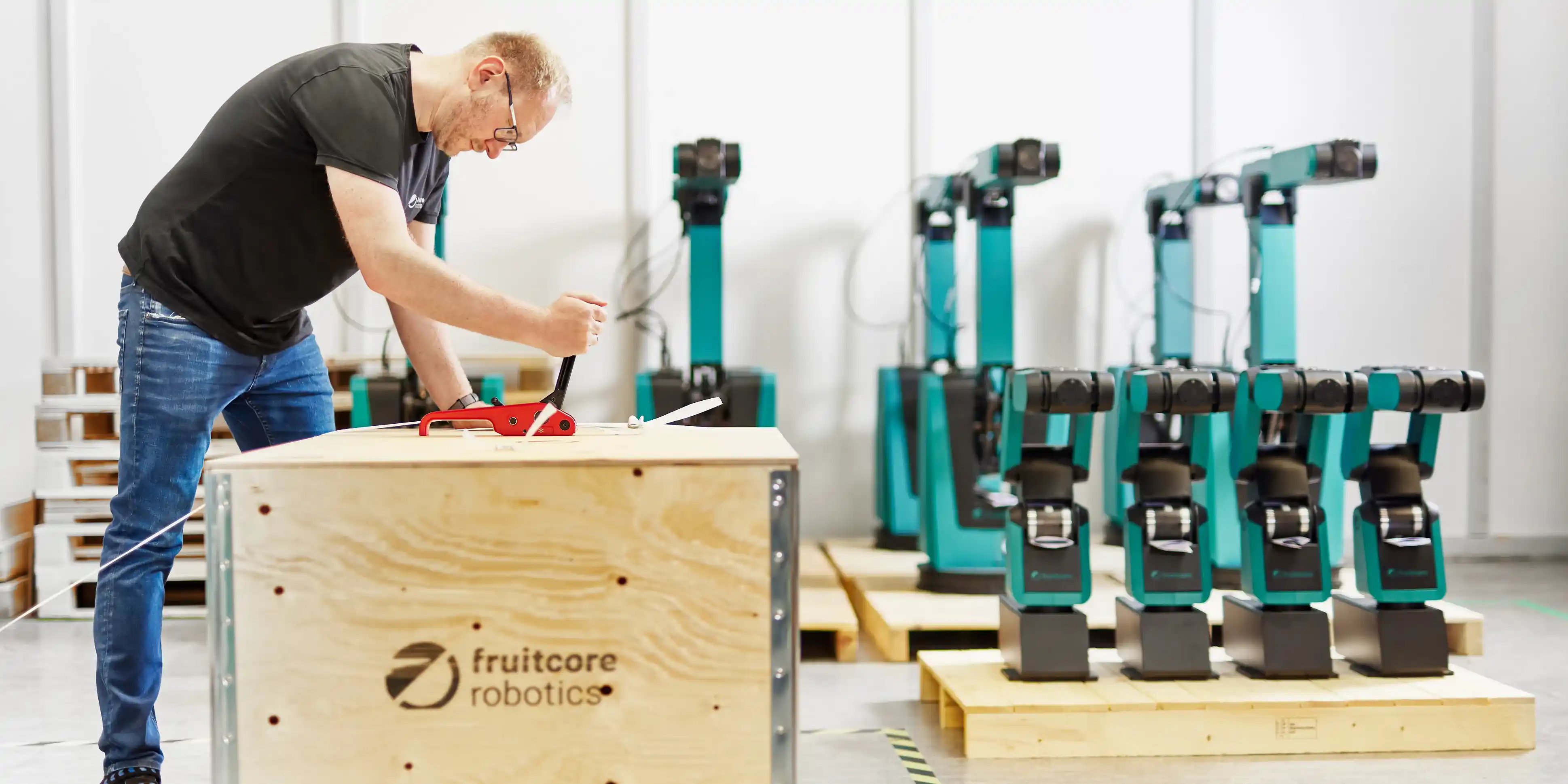
2022 was one of the most turbulent years in recent memory, with numerous economic dynamics, some of which were unexpected or are now becoming increasingly apparent. What did the year hold in store for industrial robots and the automation of production? And what direction will it take in 2023?
More industrial robots installed than ever before
The year was a record year for automation. After two years of rather weaker growth rates in newly installed industrial robots due to the Corona pandemic, robot sales now picked up strongly again: Just under 520,000 new units were added in 2021, and the industry association International Federation of Robotics (IFR) expects 570,000 for 2022. By 2025, the number of new industrial robots is expected to reach almost 700,000 a year.
In Germany, too, more new robots have been installed than in previous years. Converted, there is noew one idustrial robot for every 25 employees. By way of comparison, automation leader Sout Korea has one robot for every ten employees. In Germany, the number of robots could also have been higher, according to industry orders. At various robot suppliers, orders exceeded production capacity. This is a problem that domestic suppliers with "Made in Germany" production have been able to avoid and continue to do so. However, the local boon cannot be compared with the Cinese boom.
In China, staff problems are already causing a robot boom
In the middle kingdom, massive investments in industrial robotics and high staffing problems have led to China overtaking the USA in terms of robot density and now ranking fifth worldwide, directly behind Germany.
The challenge of a lack of employees equally demonstrates the potential and need for action in Germany, where small and medium-sized enterprises (SMEs) in particular are still shying away from the path to automation. Usually, this is because they do not consider investments in industrial robots to be cost-efficient and/or the handling of robots to be too complex. According to surveys, German SMEs do not lack interest in automation.
Especially since the rampant shortage of skilled workers and labor will become even more acute in ths country. Just think of the retirement of the baby boomer generation and the lack of young talents for traditional production activities.
The hype around cobots
A welcome solution for many SMEs seems to be cobots (also called "collaborative robots), which are not only much cheaper than conventional industrial robots, but are also easier to operate. The main feature, however, as their providers aggressively promise, is that humans can work hand in hand with a cobot without any problems; even touching is possible thanks to the built-in, sophisticated sensor technology.
The catch in practice is that cobots are much less powerful than industrial robots when working directly with humans; for safety reasons, they have to reduce speed and the application of force in collaborative mode.
Digital Robots fill the gap between classic industrial robots and cobots. In addition to the hardware, their focus is on sophisticated yet easy-to-use software and networking via the Industrial Internet of Things (IIoT). On the one hand, Digital Robots are less expensive than industrial robots, and on the other hand, they are more powerful than cobots when it comes to actually collaborating with humans.
Robots from Germany: new suppliers on the advance
For a long time, the market for industrial robots was dominated by a few manufacturers. There was no real competition for these global players - a considerable proportion of which come from Asia or have relocated their production there. The niche for industrial robots was too small, and only larger corportations could afford them, for example in car production.
That has changed, and the interest of companies with much smaller numbers of employees or production is growing rapidly. And with it, the need for manufacturers who want to communicate with SMEs at the same level, know and understand their challenges, and also want to be a partner to small businesses in automation.
This is recognized on the one hand by SMEs themselves, which are increasingly approaching these young, (still) smaller robot suppliers and placing their trust in their systems. But it is also recognized by the financial market, which in 2022 invested in German robot manufacturers several times and in some cases on a long-term basis. The VDI Nachrichten, for expample, judges the fresh wind in robotics: "In general, start-ups in the automation industry are currently very popular with Business Angels."
The future of industrial robots (also) belongs to software
For decades, automation was driven by hardware. It was primarily about robust and powerful industrial robots that could sometimes lift parts weighing tins from vehicle production. More than ever, the development towards Industry 4.0 is putting the focus of automation on software and connectivity to the IIoT.
Behind the physical hardware heart of a modern industrial robot is also digital software brain. This means that today's robots can be commissioned via a digital twin that maps its real brother in real time. The graphical programming that this makes possible means that companies no longer need and experts for robot coding. Digital Robots, for example, can be handled by an employee after just a few minutes.
Networking with the IIoT also makes maintenance easier to plan (predictive maintenance) and makes it easier to integrate robot systems into the existing production chain.
Which trends in automation can be expected in 2023?
Forecasts assume that the digitization of production will continue to increase. Industrial robots can be easily integrated into a company's processes - from ordering goods to delivering the product - using IIoT.
The user-friendliness of the operating software will be further simplified; already now, for example, Digital Robots can be operated as easily as a smartphone. The future will see more and more robot operating systems that have multiple apps or programs.
The issue of a shortage of skilled workers will continue to grow - regardless of Corona or global economic crises. With cost-effective and simple robot systems, industrial companies can respond to this without having to wait a long time for initial automation projects.