3 min read
Drives for industrial robots: It's also possible without expensive gears
Benjamin Kreuz
:
Dec 16, 2022 3:59:00 PM
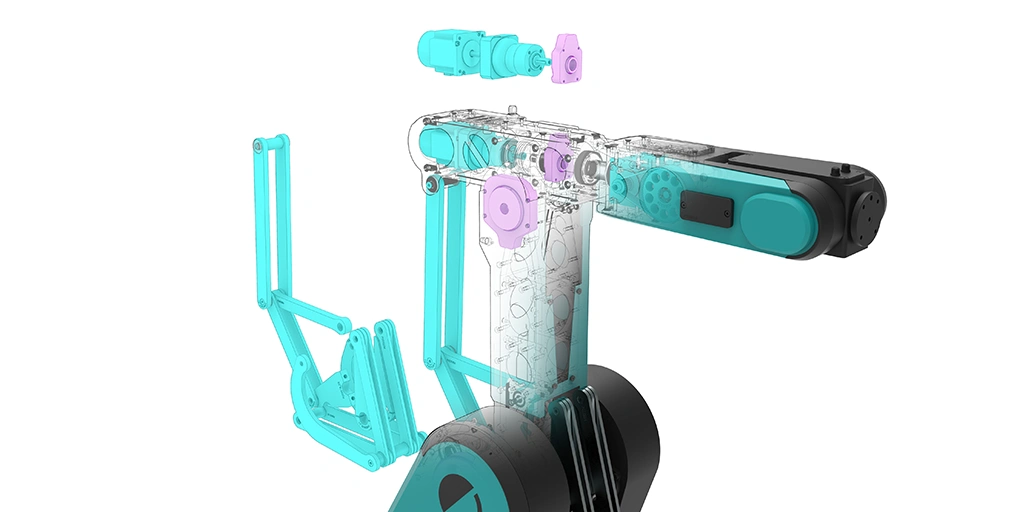
More and more industrial companies aim to automate their production. Thanks to innovative kinematics, the costs of industrial robots can be reduced. This clears one of the biggest hurdles for entering automation. Modern robots can operate without complex and high-priced mechanics.
Gear technology as a cost driver for industrial robots
With the increasing interest in automation, there is a growing demand for industrial robots that can be quickly deployed and easily operated. Some manufacturers are addressing this by advancing their robots to offer alternative drive options. This means that companies do not need to allocate time and personnel resources for their initial successful automation projects.
Even with all the simplicity and user-friendliness achievable today, industrial robots remain highly complex systems with powerful drive technology. Quality products cannot be obtained without a certain level of investment – in robotics, "cheap" rarely translates to "affordable".
One of the main cost drivers of robots is gear technology. Some providers opt for specialized gears with specific tooth designs. However, the two conventional drive concepts with shaft gears, which are often used in cobots, or cycloidal gears are also expensive. On the other hand, they are nearly free of backlash, a crucial factor in robotics. Through the development of newer generations of robots, excellent performance can be achieved at a better price-performance ratio.
How can robots do without expensive drive mechanisms?
For example, Digital Robots from fruitcore robotics are moved on the two main axes through coupling gears and planetary gears. It is particularly the patented arrangement of the coupling gear that allows load capacities, ranges, and dynamics to be achieved that would otherwise only be possible with shaft or cycloidal gears. This enables handling high loads of up to ten kilograms and a maximum range of nearly 1.50 meters. However, this is achieved without the high acquisition and operating costs of shaft or cycloidal gears.
The links of the coupling gear are arranged in a way that they transmit a significant amount of force whenever the position of the robot requires it. Consequently, the gear ratio is lower when less force is needed.
How do transmission and power transmission work in robots with coupling gears?
The significant difference of a position-dependent, non-linear drive becomes evident when compared to a linear gear mechanism: In a coupling gear system, the crank corresponds to the small gear, and the rocker to the large gear. When the crank is uniformly rotated, the rocker turns non-linearly, meaning it moves faster at some points than at others.
This, in turn, analogously affects the power transmission:
- Fast movement of the rocker = small translation = lower power transmission
- Slow movement of the rocker = large translation = higher power transmission
With this drive, the torque during acceleration under load on an extended robot arm is significantly lower than that of conventional robots. As a result, alternative drives can make do with smaller, lighter motors, which in turn keeps the price attractive.
Due to the innovative kinematics, a portion of the acting forces can be directed onto the structure via the bars. This effect is known in architectural construction from truss structures. As a result, less mass needs to be moved overall. Additionally, it is possible to place the motor for the third axis in the robot's base - this weight does not need to be moved. Overall, the drive performance can be much better utilized compared to an industrial robot with serial kinematics.
How can excessive backlash be avoided?
The Digital Robots from fruitcore robotics differ at first glance from conventional industrial robots due to the interaction of coupling and complementary planetary gears on some axes.
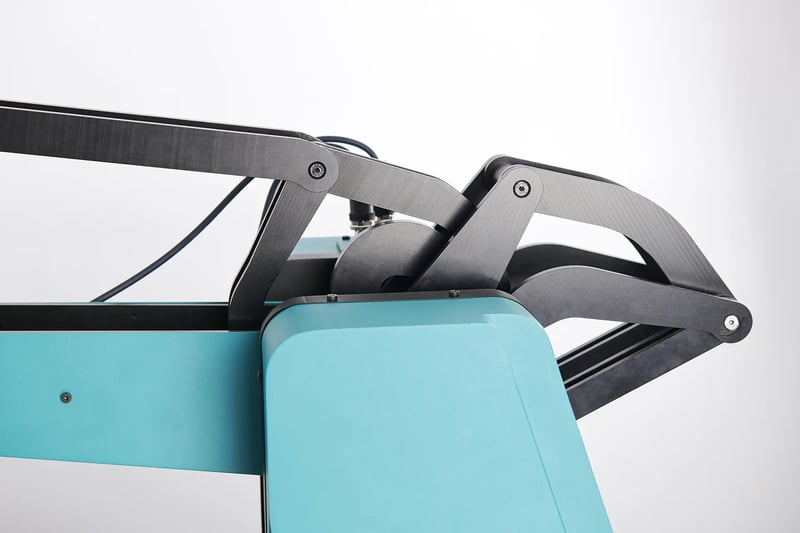
This amplifies the effect of the non-linear drive, multiplying the gear ratios. Even at high speeds of the robot, optimal load capacities and ranges can be achieved. The combination with coupling gears allows for the omission of a second gear stage in the planetary gears. This would cause an undesirable high level of backlash for articulated arm robots.
In this way, it is possible to avoid the nearly backlash-free but expensive shaft or cycloidal gears. After all, planetary gears are much more affordable due to their mechanical design and widespread use in other industries (e.g. in the automotive and bicycle sectors).
How does the lifespan differ from that of shaft gears?
Robots can operate particularly efficiently and accurately, even at high speeds, when the encoder (also known as an angular transducer) is placed behind the gear, rather than in front of it. Despite all the advantages of backlash-free shaft and cycloidal gears, their higher wear compared to planetary gears should not be overlooked: Depending on usage, the latter have a lifespan five to seven times longer.
In conclusion, even without shaft or cycloidal gears, performance levels equivalent to a conventional 6-axis robot can be achieved. Thanks to the previously untapped combination of coupling gears, planetary gears, and high-resolution encoders, Digital Robots like HORST not only offer a strong price-performance ratio but can also operate with high load capacities, ranges, and speeds. They are just as capable in terms of size and reach of the workspace as other multi-axis industrial robots.