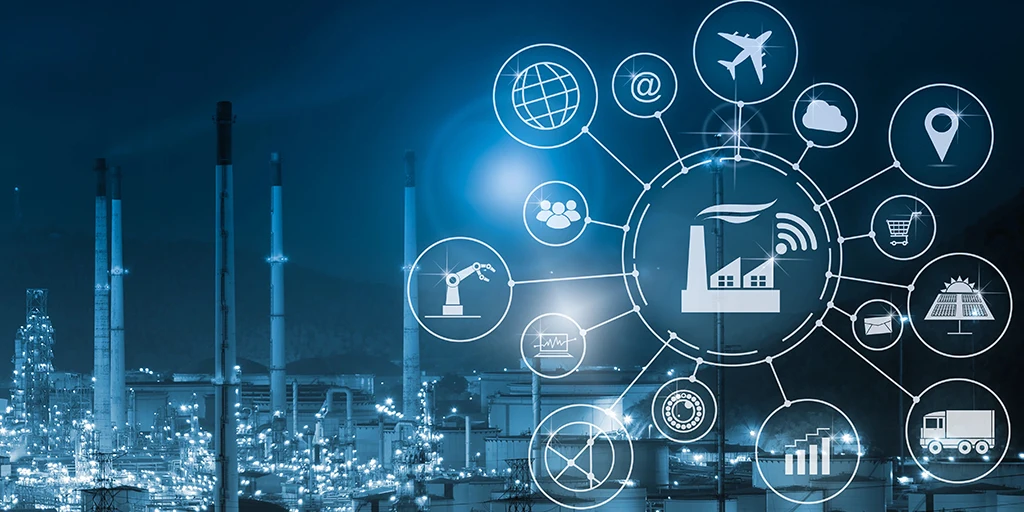
Industrial companies are facing more challenges than ever today. In order to remain successful in the long term and thrive in the competitive market, they must respond effectively to factors such as increasing cost pressures, a severe shortage of skilled workers, and digitization.
These and other factors will determine the difference between success and failure in the future. Here, you will learn more about the key challenges facing the industry.
1. Cost reduction
Companies must constantly seek ways to reduce their costs in order to remain profitable and increase their profit margins. This can be achieved, for example, by implementing more efficient production processes or utilizing automation. Additionally, costs can be lowered by minimizing waste and efficiently managing materials and resources.
When costs are reduced on the periphery of the manufacturing operation, products can be offered at lower prices without compromising quality.
Companies that are unable to do so may face difficulties in competing in the near future. Conversely, lower costs can help retain customers and provide companies with the means to invest in new technologies, such as automation.
2. Mitigating the skilled labor shortage
In nearly all sectors of the economy, there is a shortage of personnel, particularly a severe lack of qualified skilled workers. The industry, in particular, is affected by this shortage for various reasons, with causes varying by region or industry. In highly developed industries like Germany, factors such as demographic shifts, an education system focused on academic pursuits for many years, or a declining attractiveness of physically demanding or monotonous tasks are evident.
Manufacturing companies can respond to this challenge with various measures. Among them, companies can strategically train and further educate existing staff to bring in the missing expertise. Secondly, it is beneficial to maintain attractive job conditions, such as competitive salaries, flexible working hours, and a modern corporate culture. Another approach involves exploring new recruitment methods (e.g., through social media or job fairs). Some companies also find suitable personnel by looking abroad. In this regard, it is up to the government to establish the appropriate legal framework.
An instrument not to be underestimated in addressing the skilled labor shortage lies in automation. For example, by working with industrial robots, labor can be relieved, unattractive tasks can be eliminated, and efficiency can be increased. The newly gained work hours can, in turn, be devoted to new tasks within the company, where human creativity remains irreplaceable.
3. Increasing productivity
Thanks to new technologies, process optimizations, and an improved network of departments, companies can increase their productivity, thereby strengthening their competitiveness.
Regularly reviewing workflows and processes helps avoid waste and inefficiency. Open communication, especially when guiding employees into a technologized and digitized work environment, ensures motivated and engaged staff. Company management should take this into account and actively promote training in handling new technologies.
Industrial companies should also engage with the possibilities of modern technologies early on if they want to avoid losing out to global competition. This applies regardless of the size of the company; the adoption of Artificial Intelligence, Machine Learning, and robot-based automation are not reserved for large corporations, and certainly no longer a utopia. Instead, they promise businesses the ability to optimize their workflows, increase efficiency, and reduce human errors.
4. Creating a safe and modern work environment
A safe and modern work environment contributes to increasing employee satisfaction and retention. It can also enhance productivity as employees can work more efficiently.
Satisfied workers naturally desire a low-risk and balanced job. It positively affects both retaining existing staff and attracting new skilled workers when a company presents itself as attractive, forward-thinking, and open to new technologies and processes.
Modern machinery and robots, along with sustainable practices, diversity, equality, and fair communication, are crucial factors for cultivating a positive image of companies in Industry 4.0. Not least because skilled workers, through automation for instance, are liberated from monotonous or even risky tasks and can dedicate themselves to more diverse responsibilities.
5. Ensuring competitiveness and future viability
Companies must constantly adapt to changing, sometimes unpredictable market conditions. This flexibility is the foundation for remaining innovative and competitive. Investments in research and development, new business models, or technologies demonstrably promote long-term economic assertion in the market.
To fortify themselves against competition, it is therefore crucial to strategically pursue the measures described above. All of them aim at ensuring competitiveness and future viability. It is evident: companies that attract qualified employees and provide them with a pleasant work environment can reduce their costs and increase productivity. As a result, they gain a strong position in the market and are better equipped to face crises. The past years have shown how crucial this has become for economic success and is likely to continue to be in the future.
6. Advancing Digitalization
Digitalization has now advanced to a point where essentially all companies, from small businesses to large corporations, can utilize it for their purposes. By implementing digital technologies, automation, or strategically managing data, companies can enhance their efficiency, quality, and sustainability.
According to a study by the industry association Bitkom, Industry 4.0 is changing entire business models in three out of four German industrial companies, not just individual processes. 55 percent of the surveyed companies emphasize that Industry 4.0 is providing a general boost to their business. Digitalization is seen as a crucial factor for maintaining competitiveness in the industrial world of the future.
Digitalization in industry encompasses various technologies, strategies, and processes. Above all, the term Industry 4.0 is prominent, describing the fourth industrial revolution, characterized by cyber-physical systems (e.g., Smart Factory), the Industrial Internet of Things (IIoT), or cloud computing. Some are already referring to the further-evolved Industry 5.0.
IIoT refers to the interconnection of devices, machines, and sensors to collect, exchange, and analyze data. This allows companies to optimize their production processes and efficiency. Thanks to cloud computing, companies can access applications via the internet that require immense computing power. This enables, for example, the scaling of one's own IT infrastructure and reducing costs for high-performance computing.
With the progress of Artificial Intelligence (AI) and machine learning, patterns in the collected data are becoming increasingly recognizable. This can contribute to further optimizing products or minimizing machine downtimes (e.g., due to faulty or untargeted use).
Many production facilities are just beginning their journey towards automation, employing industrial robots for their tasks. This has been shown to increase efficiency, reduce errors, and make production more flexible. Some robot and machine manufacturers are already working with the concept of the Digital Twin to operate their products. These virtual replicas of physical objects allow for simulating, analyzing, and optimizing production processes.
7. Implementing Automation
It is inherent that automated production is faster and more efficient than manual labor. After all, robots and machines can work around the clock without breaks, unlike humans. In connection with this, waste can be minimized because faulty products (for example, due to lack of concentration or insufficient training) become less frequent. Automated systems work more accurately and with consistent quality across a variety of applications.
While the initial investment in automation may seem high, it often pays off for companies in as little as a year due to the high labor costs in high-wage countries. When monotonous or even risky tasks no longer need to be performed by humans, safety in the production hall increases, and accidents can be avoided. Furthermore, the company positions itself as innovative when it comes to attracting new employees.
Thanks to advancements in automation, a complete overhaul of production is no longer necessary. With modern robots and machines, initial projects can be implemented in a short period. This helps newcomers to the subject matter, but also saves time for those with existing automation expertise, creating opportunities to transfer this know-how into the practice of almost any company.
8. Additional challenges
The points described above are only the key challenges faced by the industry. When companies address these, they are already on a very good path. However, there are still other (mega) issues that should be taken into consideration. Consider, for example, globalization, the demands of customers for ever-better, individual yet still affordable products, as well as the increasing threat of cybercrime. Despite all the benefits that come with a digitized and interconnected production, companies should always pay attention to how their data is handled, where it is stored, and ensure they retain control over it.
Additionally, rising environmental and sustainability requirements, as well as new or altered (inter)national regulations and laws, should be mentioned. Since the Covid-19 pandemic or new conflicts in Europe, supply chain management has also come back into focus. There is a trend towards reshoring towards company headquarters to avoid disruptions in production processes and to be able to deliver on time.
Explore the future of industry - Smart robots for your business!
Our recommendation for successfully tackling these challenges: Consider the deployment of a simple, flexible robot for your industry! We provide tailored solutions that contribute to cost reduction, increased productivity, and a safer working environment.
Learn more about Industrial robots and how they can help you