Buying industrial robots: Everything you need to know
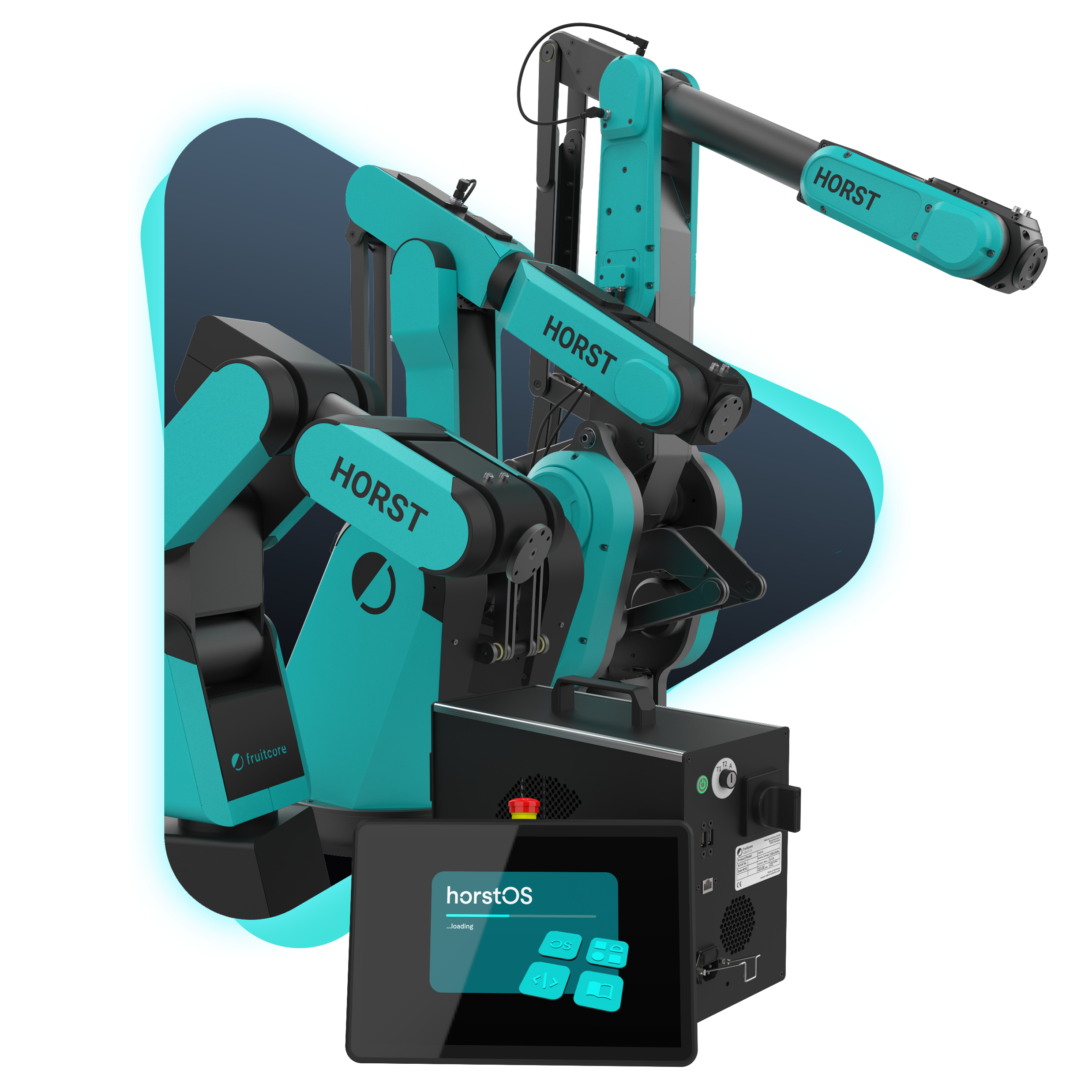
Table of contents
Introduction
Industrial robots are like super-powered helpers for any business involved in making or moving physical products. They’re flexible, increasingly smart and easy to use, and can keep going 24-hours a day. Robots make less mistakes, are flawlessly consistent, and can work safely with hazardous materials and in dangerous conditions.
In the context of ever-more challenging circumstances for industrial businesses, the return-on-investment for businesses that use robots is usually clear to see: industrial robots boost efficiency and help businesses produce more product, and they ensure high quality as they do so. Because they are a flexible tool that can be equipped with a huge array of sensors, grippers and attachments to fit almost any process, they can be adaptable over time as a business’ needs change.
The cost savings and productivity benefits of robots quickly outstrip the cost of acquiring them.
But that’s not to say the costs of acquiring robots is trivial or without risk. For small or medium-size businesses, choosing whether or not to invest in industrial robots as part of a manufacturing or production process can still be a difficult decision to weigh up.
How do you decide whether an investment in robots is the right thing for your business? The information that follows aims to help.
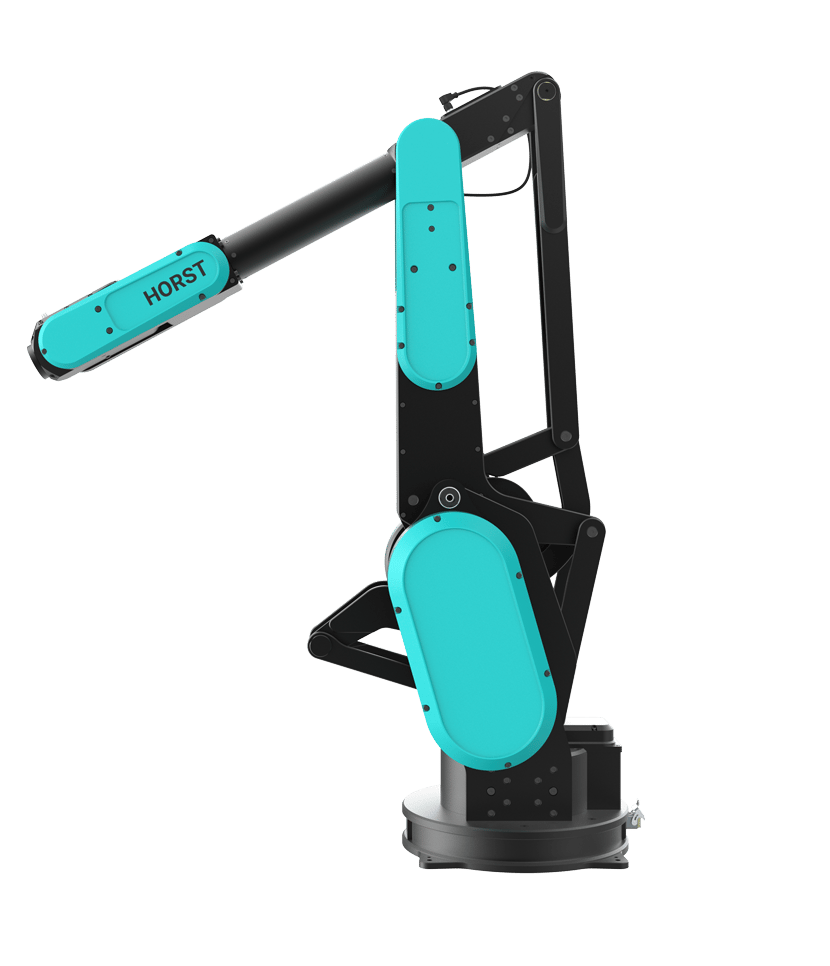
What are industrial robots?
Since the industrial revolution, businesses have sought ways to use machines to automate processes that would be far less efficient with human hands. This has taken the form of machines to carry out straightforward, step-by-step processes faster, more consistently, more continuously, and in higher volumes than any team of humans could manage. Over time, these machines became more complex and capable, and chained together they could automate large parts of many industrial workflows. But these machines are not industrial robots.
An industrial robot is defined by the fact it is programmable. It can be inserted into a process and thanks to its flexibility of movement along multiple axes, can be programmed to carry out a wide variety of tasks in a wide range of environments. Importantly, they can be reprogrammed at any time to adapt to changing requirements.
Industrial robots exist in a wide variety of forms (more on that below), but all offer a straightforward return on investment to any company that seeks to manufacture or move goods at volume.
At a glance
An industrial robot is a programmable machine that performs various tasks due to its flexible movement. It can be reprogrammed to adapt to new requirements and offers a clear return on investment for companies in large-scale manufacturing or logistics.
Why should you buy robots and automate?
Companies of all sizes opt to use industrial robots to automate their processes for several compelling reasons.
Automation through industrial robots enhances efficiency and productivity by speeding up production and reducing lead times. And once they’re going, robots can operate continuously without the need for breaks, leading to faster throughput and higher output levels.
Industrial robots improve the quality and consistency of products by carrying out repetitive tasks with precision. Errors are minimised in manufacturing processes, resulting in higher-quality products that meet stringent standards and customer expectations.
Automation with robots helps companies tackle problems they may have with labour shortages, as well as help mitigate other people-related challenges and costs that arise through recruitment processes, training, and managing staff turnover. By automating repetitive or physically demanding tasks, companies can move human workers onto more valuable things that no robot can do: sales, problem solving, customer service, creative work, or strategic planning.
Industrial robots can perform dangerous tasks and handle hazardous materials and in doing so reduce the risk of workplace accidents and injuries. This not only protects employees but also minimizes potential liabilities and costs, such as providing advanced training for employees or insurance costs for the company.
Automation with industrial robots enables companies to remain competitive in a global marketplace by reducing manufacturing costs through improved efficiency, lower scrap rates, and optimal use of resources. This cost-effectiveness allows companies to offer competitive prices while maintaining their profit margins. This is particularly true for small and medium sized businesses, especially as the overall cost of robotic solutions has reduced over time and with the availability of flexible leasing options and modular solutions to make integration easy even in very bespoke workflows.
How much do industrial robots cost?
The answer to this question depends very much on the type of robot, the complexity of its application and process they are being integrated with, the attachments and peripherals used, and the amount of human skills needed to set up and operate it. And let’s not forget energy costs, on-costs like training and insurances, and maintenance and disposal costs.
There are lots of variables, so prices can range from the low tens of thousands and up into the high six figures.
Ultimately, however, the lifetime cost of industrial robots is something quite specific to each company. Manufacturers such as fruitcore can take a detailed look at a company’s needs and help them understand total costs, calculate the time to a positive return on investment, and recommend the most cost-effective solutions. That may even include a lease option to allow company’s time to assess their automation solution before committing to long-term investment.
For a more detailed look at the costs of industrial robots, read our white paper on that subject here.
Delta robots
These robots are designed to work very fast, but within a limited area of operation. The main body of the machine and most of its weight is positioned above three or four slender arms. These arms can carry out more delicate tasks quickly, such as pick-and-place operations while assembling products or packaging items in food or electronics industries. They are limited in movement to a cone-shaped area under the machine, and cannot handle heavy materials, so are only useful for small, lightweight applications.
Cartesian/Gantry robots
These robots operate on a three-axis Cartesian coordinate system (X, Y, Z) and move along straight lines. Their range of movement is limited to the ‘box’ in which they are contained, and they’re most commonly used for tasks requiring high precision and repeatability, such as CNC machining. A 3D printer is a good example of a Cartesian robot.
SCARA robots
A common type of robot, a SCARA (which stands for Selective Compliance Articulated Robot Arm) robot is able to move around within its area of its reach to quickly manipulate objects along a limited horizontal plane. While they are often smaller and cheaper than other forms of industrial robot, they are not able to move along the Z axis. Imagine using your elbow and wrist, but your shoulder is locked to hold your arm horizontally at all times. They can be very fast and consistent, but their range of applications is limited.
Mobile robots
These robots are equipped with wheels or tracks – or even legs - allowing them to move autonomously within a facility. They are used for tasks such as material transportation, inventory management, and surveillance in warehouses and factories. Examples include flat-bed or fork-lift vehicles utilising a range of sensors to manoeuvre around a warehouse, up to more cutting-edge machines such as Boston Dynamics’ Spot and Atlas legged robots, although the practical use cases for such machines – let alone a return on investment – remains unclear for most.
Fully articulated industrial robots
The most flexible and broadly useful form of industrial robot are those that are fully articulated arms with six axes of motion, closely modelling the range of motion we can achieve with our human arms. These robots can be programmed to carry out a huge array of tasks. There are three broad categories of fully articulated robot arms:
-
High precision or payload robots:
Machines with very highly engineered motor and gear systems designed to shoulder heavy loads, achieve very high precision, or both. These are the sorts of industrial robots familiar in contexts such as automotive manufacturing, handing bulky materials, palletising, or loading and unloading heavy machinery components. Very high-grade precision engineering of motor and gears means these industrial robots can achieve extremely accurate movements for use in precision assembly, intricate machining or delicate manipulation of parts. The engineering involved does, however, mean that the cost of purchase and maintenance is high, making them less suitable for small or medium sized businesses.
-
Collaborative robots (cobots):
Combining the versatility of articulated arms with collaborative capabilities, cobots are designed to work safely alongside human operators without the need for safety fencing. They are utilised in applications such as assembly, inspection, and packaging, where human-robot collaboration enhances efficiency and flexibility on the production floor. Cobots are loaded with advanced sensors and control systems to ensure they can operate safely around humans, meaning they are typically more expensive and operate at much slower speeds than other robots.
-
Intelligent industrial robots:
Fully articulated six-axis robots designed to be applied on the shop floor quickly in combination with user-friendly, low- and no-code software that dramatically lowers the barrier to entry for businesses aiming to automate their workflows. Modern intelligent robots are characterised by using innovative, lower-cost drive systems than the expensive high-precision robots used in big industry, while avoiding the significant cost and speed limitations of Cobots. A highly modular approach and pre-built programs helps companies deploy these smart robots quickly, while supported by a robots-as-a-service operating model and flexible ‘rent-a-robot’ leasing terms.
-
Cognitive robots:
Robots in a variety of form factors – from wheeled mobile machines and articulated arms to bi-pedal humanoids – that are distinguished by possessing a wide array of sensors and advanced AI capabilities that allow them to perceive, learn, and interact with their environment in a human-like way. Cognitive robots can adapt to dynamic or unpredictable situations, reasoning out solutions and making decisions on their own without the need for additional programming. A key feature of cognitive robots is their ability to interact with humans via natural language processing and gesture recognition; they can engage in dialogue with humans and understand commands.
How do you choose which type of robot is best for you?
Read our white paper for more information.
What are the applications of industrial robots?
Industrial robots, especially extremely flexible systems such as the modern and intelligent robots, can be turned to a huge variety of tasks. The chances are that if you have an industrial process, a robot will be able to bring you fast increases in productivity and a positive ROI quickly. Here are some examples:
- Loading and unloading machines
- Part separation
- Quality control
- Glueing and dispensing
- Assembly
- Pick and place
Find out more about these applications here.
What is meant by smart industrial robots?
The new innovative robots such as our own HORST platform are designed to be companies’ ‘companion in automation’. The latest hardware technology meets the most user-friendly software. Industrial robots like HORST aim to help companies achieve a very fast return on investment, particularly if they are just beginning their automation journey or are smaller or medium sized businesses aiming to reap the productivity benefits of industrial robots as they grow.
As the leader in digital robot technology, fruitcore robotics keeps a very close eye on how its customers progress as they undertake their progress, and we can confidently say that the advantages of robots like these are clear.
Latest robotic technology: These machines are economical, long-lasting, and low service, unlike more expensive industrial robots. HORST features a patented and unique drive system that allows companies to achieve high performance for industrial applications, 24/7, at a much lower entry cost.
Central control software: HORST-systems feature easy to use control software that mitigates the high cost overheads of programming traditional industrial robots. Individual components or entire processes can be operated intuitively via simple pre-packaged interfaces.
Pre-configured automation modules: Pre-built programmes and component kits for typical use cases, as well as array of plug-and-play interfaces, mean these modern robots can be quickly set up to handle an almost limitless array of tasks in an industrial process.
Traditional industrial robots vs modern industrial robots
In many situations, innovative systems such as those provided by fruitcore robotics offer several advantages over traditional industrial robots.
fruitcore robotics’s HORST robot product family use patented drive technology to deliver the accuracy and performance required of a top-tier industrial robot but at a fraction of the cost. Outside of the heavy-load or long-reach requirements of large-scale manufacturing, HORST robots are an ideal automation solution in most circumstances, particularly for small or medium enterprises (SMEs).
Traditional, highly-engineered robot systems are ideal for automating tasks in very large-scale operations where a return on investment can be achieved with high volumes over extended timeframes. They require costly setup, highly specialised operators contracted or on the payroll, and expensive ongoing maintenance, meaning they are less useful for companies that aren’t working on a very large industrial scale. Smart and innovative robots mitigate all of those overheads to make a quick, positive ROI achievable for medium sized companies.
An important part of how robots such as HORST are able to be deployed quickly is the software and services they come packaged with. Programming and operating is done via intuitive graphical user interfaces, assisted by AI, and with a service model that affords users continuous support from the manufacturer form initial scoping and installation through to day-to-day operations and problem solving.
The disadvantages of traditional industrial robots
High-end, high-precision industrial robots offer advanced capabilities but pose challenges for small and medium-sized companies (SMEs).
The substantial upfront investment required, including the cost of the robot, specialized tooling, and integration, can strain limited capital resources. Implementing these robots is complex and demands expertise in programming, system integration, and staff training, which SMEs may lack. Maintenance and support costs add to the financial burden, and finding skilled personnel for operation and programming can be difficult.
Moreover, the inflexibility of high-end robots, optimized for specific tasks, may not align with SMEs' varying production needs. Dependence on a limited number of suppliers with large operations and typically long supply chains and long lead times for components, are additional concerns, meaning SMEs may struggle to achieve cost-effectiveness and efficiency comparable to larger enterprises.
Despite their precision and performance, high-end robots may not always be a feasible or practical choice for SMEs.
The disadvantages of cobots
Collaborative robots (cobots) offer benefits like flexibility and safety, but they come with certain drawbacks. Their limited payload and speed make them unsuitable for tasks requiring heavy lifting or high-speed operations, where operating at high speed is usually one of the main reasons businesses would invest in an industrial robot in the first place.
The higher initial cost of cobots may be a barrier for SMEs with limited budgets. Additionally, cobots have a smaller reach and workspace compared to traditional industrial robots, limiting their applicability in certain environments.
Safety considerations are paramount for cobots as they work alongside humans and pose potential risks such as collisions or entrapments. Their dependency on human interaction naturally introduces variability and inefficiencies into production processes. Integration challenges and more complex maintenance requirements further add to the difficulty of adopting cobots. Despite these disadvantages, cobots can offer advantages in flexibility and ease of use in specific circumstances, making them valuable automation solutions for businesses willing to carefully evaluate their suitability and invest in proper implementation and training.
At a glance: The benefits of smart robots
Robots like our HORST platform serve as companies' automation companions, blending advanced hardware with user-friendly software. fruitcore robotics's HORST robots use patented drive technology to offer top-tier industrial performance and accuracy at a lower cost, providing several advantages over traditional robots.
How are robots operated?
Industrial robots are technically operated through a combination of hardware, software, and human input. The process begins with the selection and installation of the appropriate robot model for the job. Operators then configure the robot's hardware components - motors, sensors, end effectors, and safety features - to ensure optimal performance and safety.
Programming the robot is a critical step, involving the creation of instructions that dictate its actions specific to the task at hand and the environment it is in. This programming can be done using various methods and varies between robot manufacturers, but typically involves using offline software and any one of a range of programming languages. So-called teach pendants are a common interface for robot programming, consisting of a usually hand-held device to ‘teach’ a robot its actions step-by-step in situ in the work area.
Traditionally, programming robots has therefore been a function of highly trained specialists, although this is changing rapidly with the advent of smarter and more flexible industrial robots and their simpler, AI-driven operating systems that don’t necessarily require specialised programming skills at all.
Once up and running and integrated with the manufacturing workflow, operators monitor the robot's performance and optimise further or address any issues that occur. They’ll also carry out regular maintenance tasks such as lubrication, recalibration, and replacing parts – the degree to which this is required depends greatly on the type and complexity of the robot in use.
Why software is crucial to make robots easy to use
A primary barrier to entry for companies that would benefit from robots and automation in their workflows is the traditionally very high overhead in terms of the technical and programming skills needed to integrate and operate them.
The perception of these costs extra to the price of the systems themselves lead many to resist making an investment in robotics. However, as technologies such as cloud computing, IoT, digital twins and now AI have emerged, the smart software platforms used to programme and operate industrial robots are now taking away much of that burden.
The types of programming languages and operating systems used by different robot manufactures vary widely and are often proprietary with their own training and certification schemes. A defining characteristic of these younger industrial robots, however, is how they are revolutionising automation with their simplicity, digital connectivity, and cost-effectiveness compared to traditional industrial robots. They are designed to be utilised for a wide range of applications without extensive robotics training, making them accessible even to SMEs.
Software interfaces for robots such as HORST are designed to be used as simply as a smartphone, eliminating the need for complex programming knowledge and allowing for easy setup and operation via touch screens.
Intelligent robots replicate entire applications through digital twins, speeding up setup and operation while connecting all integrated components within the robot system. Since this new breed of software has been developed at the same time as the robots themselves, they are not built on a legacy of older technologies that lead to added complexity and the need for expensive specialist knowledge.
"Digital Robot" software also benefits from continual over-the-air updates as part of the servitised package offered with these robots.
How robots are used in manufacturing
Industrial robots are extensively used in manufacturing across various industries, ranging from automotive and electronics to food and beverage production. They perform a wide range of tasks, including assembly, welding, painting, packaging, and material handling, among others.
In larger operations, robots typically operate alongside conveyor systems and other automated equipment, seamlessly integrating into the production line to streamline processes and minimize human intervention. They can work 24/7, reducing cycle times and increasing throughput while maintaining precision and accuracy.
Industrial robots are increasingly becoming accessible to SMEs in the manufacturing sector due to advancements in technology and the availability of more affordable and user-friendly robot systems.
SMEs often use robots to automate tasks such as pick-and-place operations, machine tending, packaging, and quality inspection. SMEs will usually work with robots that can be deployed in flexible manufacturing environments, where they can be adapted quickly to changes in production requirements and handle diverse and changeable product portfolios. This is particularly useful in the context of plastics, where requirements can change quickly and batch sizes can be small.
How robots are used in education
Industrial robots are valuable tools for teaching various aspects of robotics, automation, and engineering. You can find robots at all levels of education, from primary schools to universities, and in training and apprenticeship schemes in private enterprises. Robots in these contexts provide students with hands-on experience and practical knowledge of robotics.
A vital practical ingredient of STEM education, students learn fundamental concepts such as automation and robot design, programming, and control.
In higher education institutions, industrial robots are integrated into engineering, mechatronics, and robotics courses, and can be used in research as well as training. Robots enable learning in the areas of kinematics, dynamics, control systems, industrial applications, robot programming languages, simulation software, and of course the robotic hardware platforms themselves.
Increasingly, especially with intelligent robot platforms such our own HORST systems, robots are also learning aids in the fields of Internet of Things, advanced data and analytics, and AI.
How robots are used in laboratories
While robots and their accompanying systems form an active basis of ongoing academic research themselves, they are also used as versatile and precise tools for conducting repetitive, complex, and high-precision tasks in controlled medical and laboratory environments.
Their tasks may include handling samples, chemical and biological analysis, materials testing, or prototype assembly. In a research context, robots are employed in lab automation duties to manage high-volume screening, sample preparation, and pick-and-place functions to dramatically increase the pace of experimentation while reducing errors.
Industrial robots are also used in laboratories as part of research and development activities for prototyping and testing new technologies and products. They can assemble parts, be used in quality control, and help with performance testing to speed up the iteration and refinement of designs.
What are the energy costs of industrial robots?
Industrial robots running continuously will obviously consume electricity, but exactly how much depends on how much movement they are doing, the payloads they’re managing, and how long they are working.
There are a number of things operators of robots can do to minimise their energy usage, and this can add up to significant savings over time.
For example, using energy monitoring tools can identify opportunities to optimise a robot’s usage to minimise energy consumption. Refining a robot’s programming can also lead to energy savings, for example by reducing moments of high acceleration and deceleration.
Choosing robots that are designed with energy efficiency in mind from the outset is the simplest way to minimise the energy costs of their operation. This will involve factors such as the energy efficiency of the robot’s drive system, gearing and components.
How easy is it to set up and run robots?
The ease – and therefore speed and cost – of setting up industrial robots depends greatly on the tasks they are performing. For example, the set up of relatively simple pick-and-place functions should be straightforward. Welding applications will be slightly more complex, with a greater number of variables and feedback controls required. Very specialised tasks, such as in prototyping or experimentation in a research-and-development context, may require bespoke grippers and novel sensors.
For all these applications, the degree to which the robot’s manufacturer offers training, support and turnkey solutions for integrating robots is a large factor. Some companies will offer a wide range of ongoing support, certainly where they are catering to smaller businesses, whereas others will be used to dealing with larger customers who already have significant robotics-operations resources to manage installation.
Smart industrial robots are designed to be as simple as possible to integrate and use quickly with a plug-and-play like approach to modularised products and services.
We have a useful white paper here for those just starting out on their automation journey.
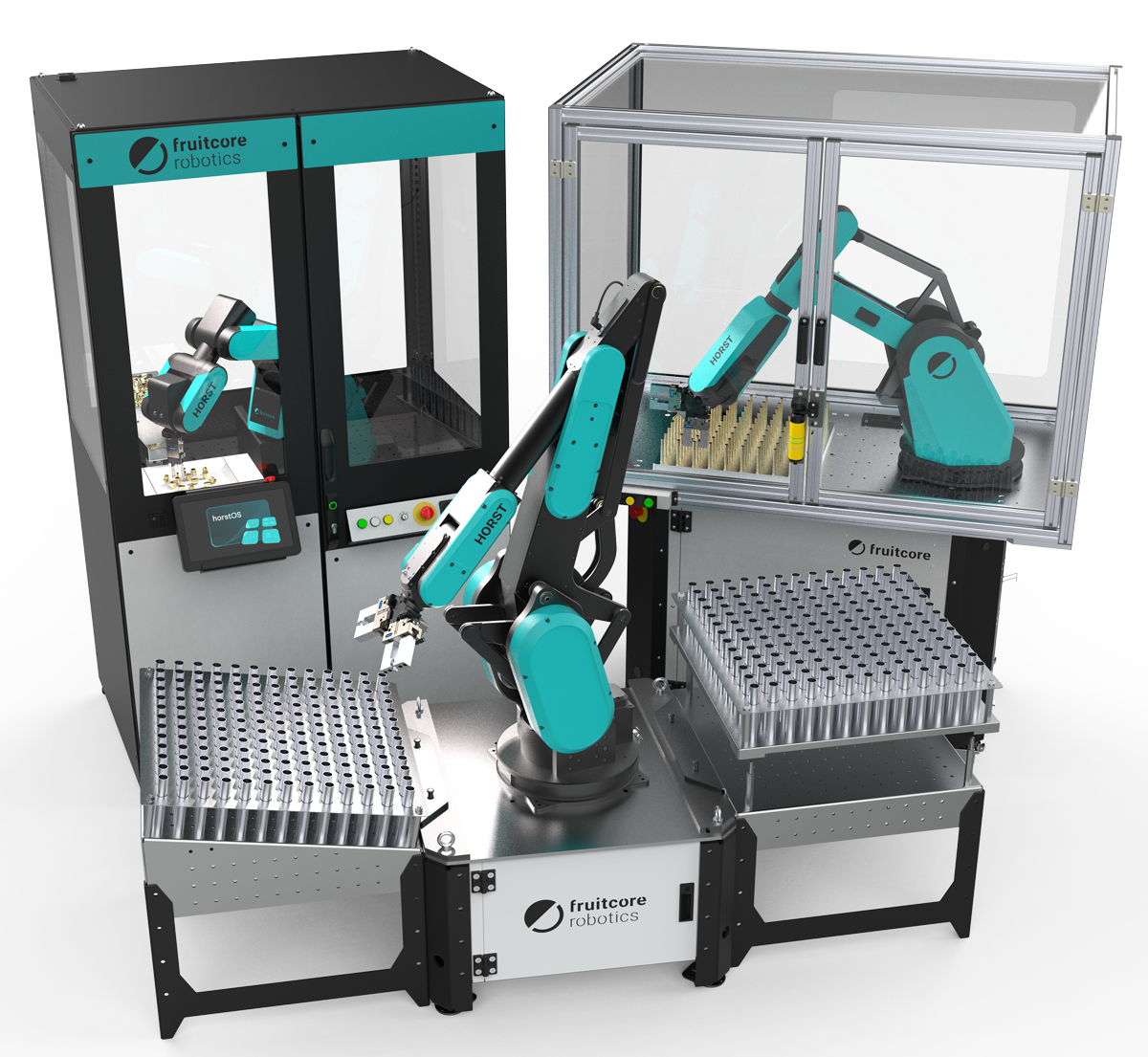
How is AI playing a role in robotics?
In a sense, AI has been a part of operating industrial robots for a long time. These days, the emergence of generative AI and Large Language Models (LLMs) is adding a new flavour of AI into the mix.
Machine learning has played a role in advancing industrial robots for quite a long time, enabling the advanced algorithms that robots now use to respond dynamically to sensor feedback. Machine vision systems allow robots to see their environment and interpret what they see, be those objects or patterns. This is particularly important for robots engaged in things like quality inspection or assembly tasks. AI can even allow robots to interact directly with humans, where machine vision and natural language processing (NLP) means they can understand and respond to human gestures or voice.
Generative AI can be extremely helpful to provide real-time assistance to robot operators. Our own horstOS central control software features an AI copilot that helps operators create and optimise their programs.
How robots drive ROI and save you money?
More and more companies are recognizing the importance of automation, not only large corporations, but also small and medium-sized enterprises (SMEs). However, a perceived complexity and supposedly high acquisition costs are slowing down the broad acceptance of industrial robots.
In 2021, only 19% of SMEs in the manufacturing industry used an industrial robot: Growth in the last three years was therefore only 3%. Across all sectors, only 4% of SMEs use industrial robots.
The reason for this is that the introduction of traditional industrial robots in the past meant considerable investment with extremely long payback periods. Fortunately, new developments such as the HORST robot systems reduce these costs enormously - and therefore also the time it takes for them to pay for themselves.
Cobots are often seen as a way of implementing robotic solutions more easily into existing processes. But they tend to be relatively expensive and, most importantly, very slow for the industrial sector. The innovative next generation of industrial robots, on the other hand, cost only a fraction of a cobot. Yet they offer performance comparable to conventional industrial robots. At the same time, they simplify automation thanks to exceptionally user-friendly software, AI integration and much more cost-effective drive systems.
The life cycle costs of a robot like HORST amount to around 80,000 euros over a period of ten years. By comparison, a conventional robot, such as those found in large-scale industry, costs at least 300,000 euros.
A very healthy ROI is very much now within reach for most SMEs. Learn more here.
Are industrial robots taking jobs away from humans?
Many people fear that industrial robots represent a threat to the jobs and livelihoods of human workers. It’s a fear that has existed for decades, but today that fear can still affect the decision making of business owners when weighing up whether to invest in robots; how will investing in robots affect their valued employees?
The truth is that studies show industrial robots have a positive impact overall on human workers in several respects. It’s a fact that’s gradually being recognised by the population at large, too, as shown in a survey fruitcore robotics conducted of people in its native Germany.
Industrial robots bring substantial benefits for a company’s efficiency, productivity, and profitability. This not only ensures the survival of the company in a competitive global marketplace, it allows the company to grow and therefore create more jobs, rather than less. Meanwhile, implementing automation itself provides opportunities to retrain and upskill existing workers.
Industrial robots also make work life safer for the humans around them, handling strenuous and hazardous tasks on their behalf, allowing the humans to focus on more value-adding tasks.
And these benefits are found against a backdrop of labour and skills shortages that are affecting most industrialised nations. Headlines may suggest that robots are threatening to replace human workers, but the truth is quite the opposite: Industrial robots have become an important way for SMEs to sustain their productivity and compete, grow employment, and overcome skills shortages.
Does it matter where your robots are made?
In today’s world of disrupted supply chains, growing conflict, economic uncertainty, and rising cybercrime, all companies have very good reasons to make their critical automation investments as local as possible.
Many robot manufacturers are either based in very far away places, or they are very exposed to component supply chains that extend just as far. If your company operates in Europe, for example, you may find that your initial acquisition costs for new industrial robots are lowered slightly by purchasing from Asian manufacturers. However, doing so will commit your company to potentially very high lead times, delivery delays, higher maintenance costs, and potentially more difficult support and communication channels.
Another factor is securing the data and operating systems of your robots once installed. Europe now features the most stringent data-protection regulations in the world, and companies must ensure the connected systems they are using are compliant with those standards ‘out of the box’ and safe against the ever-increasing threat of cyber attacks.
The future of automation
Industrial robots boost efficiency, productivity, and profitability, fostering company growth and job creation. They enhance workplace safety by handling strenuous tasks and offer retraining opportunities for workers.
Amid labor shortages, robots help SMEs maintain productivity and compete, countering the myth that they replace human workers. Due to supply chain disruptions and economic uncertainties, investing locally in automation is crucial. Though Asian manufacturers may have lower initial costs, European companies face risks of long lead times, delays, higher maintenance costs, and communication challenges.
Robots for any purpose: How to make robots work for you
Many SMEs may resist the idea of automation because they assume their processes are too unique for robots to easily manage. Perhaps they are very bespoke or delicate processes, built through painstaking trial and error, and it seems inconceivable that robots could be tailored to help scale these special circumstances to greater volumes.
Today’s industrial robots, however, are made to be incredibly flexible. Innovative industrial robots are designed to be a cost-effective and hugely customisable solution for scaling companies. As well as AI-driven and easy-to-use operating systems, hands-on consultancy is provided from the beginning to assess the feasibility of automation in every situation. Solutions are then provided in the form of modularised kits, which are assembled, cabled, programmed and configured to get up and running fast.
It is even possible to lease this service on a short-term basis for companies to test the systems and ensure they can achieve the results they need.
Examples of robots in use in SMEs
A wide range of SMEs are using industrial robots in a variety of different ways. There are as many specific tasks for robots as there are things to be produced by different companies.
Here are a few examples to study.
CyFa-Tech.ch Manufacturing Solutions
This small Swiss company – just six employees - specialises in CNC turning, milling and measuring, creating components for other manufacturing processes. They used a HORST system to mange the loading and unloading of their CNC milling machine, doubling their production output and dramatically increasing turnover. Their HORST robot paid for itself within three months.
Ask an Expert
A big part of fruitcore’s mission to help companies take big steps forward with intelligent automation systems, and we’re here to help. Whether we are the right solution for you or not, we are ready to help you understand the pros and cons of industrial robots for your business.

fruitcore robotics GmbH
Macairestraße 3
78467 Konstanz
+49 (0) 7531 976 240
info@fruitcore.de