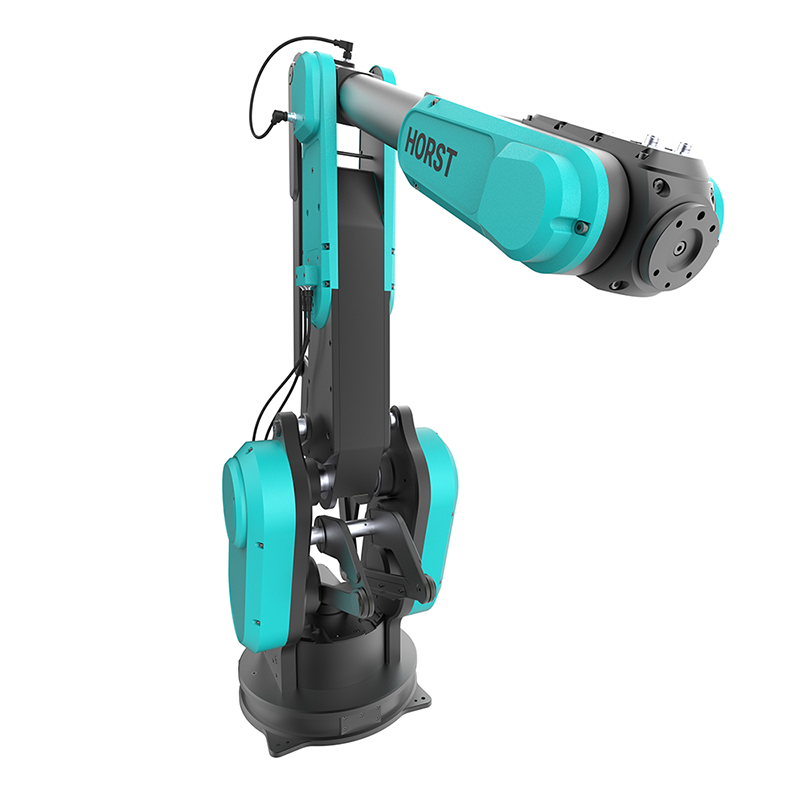
fruitcore robotics presents HORST1500, the new generation of its digital robots
fruitcore robotics, a pioneer in the field of AI-supported automation solutions, is expanding its...
With the Digital Robot Platform, fruitcore robotics offers all the building blocks for optimized automation in industry - from project planning to ongoing operation.
In addition to AI-supported industrial robots, the Digital Robot Platform also includes central control software, preconfigured automation modules for a variety of use cases and supporting services.
Our service includes free feasibility studies and comprehensive training concepts (live and on demand). We support you until the robot is working productively with the support of our application technology on your premises.
Master all challenges with HORST:
Immerse yourself in the world of intelligent automation with our innovative industrial robots, unique software, versatile ecosystem and outstanding services. Optimize performance in almost any industrial application and free your employees from monotonous tasks.
Are you aware of the challenges of achieving greater efficiency, quality and productivity? Have you identified processes in your company that could potentially be optimized? We invite you to join us in taking a closer look at potentially overlooked risks and problems in industrial production - from precision in pick and place to inefficient separations and inaccurate quality controls. We also consider specialized processes such as gluing & dispensing and their impact on the success of your operation.
Ready for the future of automation: CE-certified and ready for immediate use
We know that time is money - especially when it comes to planning and commissioning automation. That's why we have developed preconfigured solution kits that save you valuable resources. With these kits, which have been specially developed for the industrial robot HORST. you can make your production agile and flexible - safely and cost-effectively.
Realize your project economically, flexibly and efficiently with our automation modules. Our solution kits offer you everything you need for your specific application: be it pick and place, parts separation, machine loading and much more! Our automation modules are available for the HORST600, HORST1000 and HORST1400 robots and offer an outstanding price-performance ratio.
With HORST, you can transform the loading and unloading of your machine tools through automation. Our ready-to-use, CE-certified automation modules are characterized by their quick installation and changeover. Thanks to ready-made graphical programs, programming work with multiple grippers has never been easier. We also enable you to control additional machines in your system cost-effectively without an additional PLC.
Our automation module enables flexible separation of a wide variety of parts, which you can expand to suit subsequent processes. You can set up new parts within minutes thanks to preconfigured software. This allows you to react immediately to changing requirements. You can seamlessly integrate automation with the Digital Robot HORST into your existing systems.
Would you like to automate your production processes in a smooth and efficient way? Then our Pick and Place Solution Kit is just right for you! This specially developed solution not only offers you intuitive operation and user-friendly software, but also enables you to optimize your production processes with little effort. With our Solution Kit, you can take full advantage of automation and increase your productivity without having to worry about complicated setups.
With HORST, training companies, schools and universities can quickly and easily get started with robot-supported automation. In addition to the complete automation module, we provide you with a practice application to learn programming in a fun way. You can flexibly adapt the ready-to-use module for pick-and-place tasks to the respective educational purposes. Teachers receive specialized training and extensive documentation for themselves and their class. The entire module is mobile and can be used with a standard household 230V power supply.
Discover the ideal combination of industrial robots, customized software and services as well as a holistic training concept. Get a quote with just a few clicks!
Which Digital Robot or Solution Kit will help you best?
Which software features give you a competitive edge?
How do you secure the best lifecycle costs with additional services?
Would you like to access our training courses?
Hundreds of our intelligent Digital Robots help companies of different sizes and industries automate every day. Let the users convince you.
Valuable information for getting a start in the field of automation or expert knowledge for the use of industrial robots in numerous industries: The HORST blog provides you with the latest topics and developments in the field of automation and robotics!
fruitcore robotics, a pioneer in the field of AI-supported automation solutions, is expanding its...
Sylvie Rest
March 14, 2024
With the new Solution Kit Part Separation with 2D Grasping-Kit, the partners fruitcore robotics...
Sylvie Rest
February 20, 2024
fruitcore robotics is rolling out a new software update for its intelligent HORST industrial...
Sylvie Rest
November 15, 2023