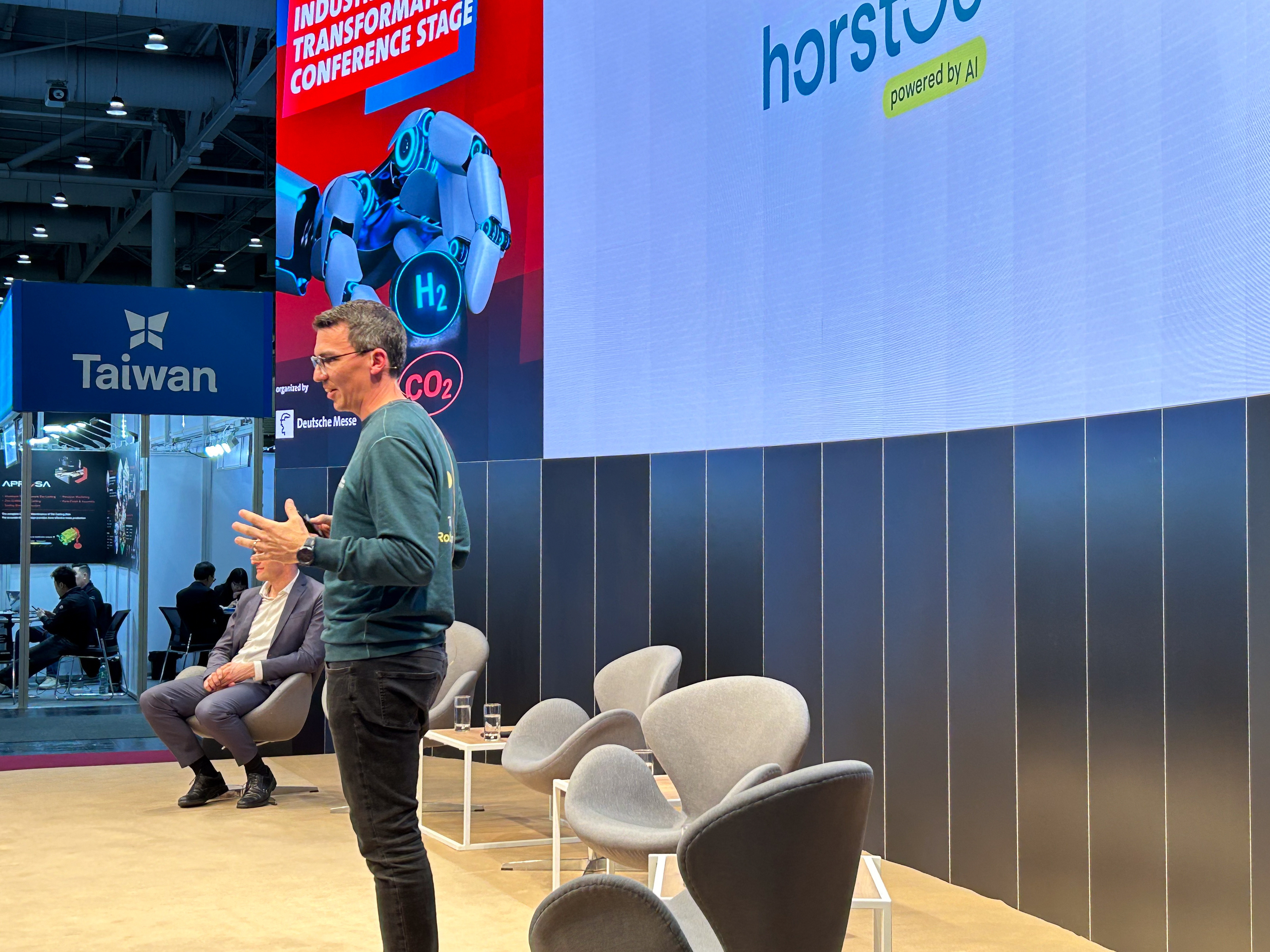
The future of industrial robotics is driven by AI
By Patrick Heimburger, Managing Director, fruitcore robotics
According to the latest statistics from the International Federation of Robotics, more than half a million industrial robots were installed worldwide in 2021 alone - a new record for the industry. In Germany, thousands of units were also added, further solidifying the country's leading position in Europe.
Geposted von:
Janik Ebner
According to the latest statistics from the International Federation of Robotics, more than half a million industrial robots were installed worldwide in 2021 alone - a new record for the industry. In Germany, thousands of units were also added, further solidifying the country's leading position in Europe.
In this article, you can find out what policymakers are hoping for from more industrial robots. You can also read about the reasons why no wave of unemployment is to be expected on the German labor market, even with automation becoming increasingly suitable for mass production.
In 2021, approximately 517,000 industrial robots found their way into companies worldwide. This surpasses the previous record set in 2018 by 22 percent. The industry globally now employs around 3.5 million robots. In Germany, with almost 246,000 deployed industrial robots, securing the title of Automation European Champion, nearly 24,000 new units were added. The largest growth compared to the previous year was observed in the metal and machinery industry, followed by the plastics and rubber sector.
These figures are from the World Robotics Report 2022 by the industry association, the International Federation of Robotics (IFR). Globally, over twice as many industrial robots are now installed annually compared to 2015. IFR President Marina Bill spoke of a "rapidly accelerating" increase in robotics and automation. The IFR anticipates continued growth in sales figures for the coming years.
The German Engineering Federation (VDMA) also recently reported a surge in demand. Frank Konrad, the chairman of the Robotics + Automation division, noted a "boom" in robotics. The VDMA expects a 5 percent increase in industry revenue to reach 3.6 billion euros in 2022. This is despite challenges faced by manufacturers, particularly those not producing domestically and relying heavily on foreign-sourced components. This is a problem that can largely be circumvented with "Made in Germany" industrial robots.
The urgent need for robot growth is unquestionable. Small and medium-sized enterprises, in particular, have a significant catching-up to do. While industrial robots are already commonplace in large corporations, only a low single-digit percentage of companies with fewer than 250 employees utilize one or more robots.
These robots can contribute to addressing the labor and skills shortage - arguably the greatest challenge facing the industry today and in the future. Aside from childcare and elderly care, technical professions are among the most affected by a lack of personnel. The scarcity of labor is a key driver for the establishment of robots in the industry, both in the medium and long term, due to declining birth rates and the advancing retirement of the Baby Boomer generation.
The urgent need for robot growth is unquestionable. Small and medium-sized enterprises, in particular, have a significant catching-up to do. While industrial robots are already commonplace in large corporations, only a low single-digit percentage of companies with fewer than 250 employees utilize one or more robots.
These robots can contribute to addressing the labor and skills shortage - arguably the greatest challenge facing the industry today and in the future. Aside from childcare and elderly care, technical professions are among the most affected by a lack of personnel. The scarcity of labor is a key driver for the establishment of robots in the industry, both in the medium and long term, due to declining birth rates and the advancing retirement of the Baby Boomer generation.
However, some critics argue that an increase in robots will lead to a mass loss of jobs in production. It is sometimes suggested that up to six positions could be eliminated per robot. In contrast, a group of researchers has downplayed this scenario for Germany, stating that such outcomes are not expected. This could be conceivable in nations with different labor market conditions and a lax protection for employees, such as in the USA.
According to current studies, the reduction in jobs in Germany is estimated to be around two positions per industrial robot. However, these positions are offset by job gains in other industries. Overall, the decrease and increase in jobs due to the establishment of robots balance each other out.
Researchers point out that, on one hand, existing personnel are not typically laid off, but rather retrained and upskilled for other tasks within the company. This results in a career advancement for the affected individuals - a win-win situation for employees and companies.
Secondly, the German industry benefits from having predominantly productive companies in international comparison. These firms, including global industry leaders of all sizes or hidden champions, increase their productivity, competitiveness, and ultimately the number of employees through new technologies, among which robots undoubtedly play a role.
Several trends enable companies that have not previously used automation in their production to join the robotics revolution. Firstly, the use of industrial robots has become increasingly user-friendly - from setup and programming to operation and contacting manufacturers for support. Among the advantages of this new generation of so-called Digital Robots are intuitive, smartphone-like operation as well as the integration of software and hardware.
For robot users, building an automation ecosystem "provides enormous added value, as effort and time until commissioning are significantly reduced," as summarized by the International Federation of Robotics. Additionally, the integration of tools or external components into the entire robotics application becomes easier, as standardized program modules - for frequently needed process steps, for example - can be integrated into the operating software.
Secondly, robots of the modern generation are no longer comparable to their predecessors. Digital Robots operate much more intelligently. The software of this innovative type of robot is constantly evolving, becoming more sophisticated and user-friendly in rapid succession. This includes the exchange and interpretation of data between robots and with machines through an Industrial Internet-of-Things platform.
Thirdly, an increasing number of companies recognize that industrial robots can be an opportunity to potentially reshore production to its original location to circumvent supply chain issues. These issues are caused, among other factors, by the COVID-19 pandemic, geopolitical tensions, resource shortages, and increasingly, global climate change.
Do you want to understand why a powerful industrial robot should also come with user-friendly software? Then, get informed in our free Whitepaper about the current capabilities of a Digital Robot. Across 12 pages, you will discover the opportunities and challenges that companies of all sizes associate with automation.
By Patrick Heimburger, Managing Director, fruitcore robotics
Patrick Heimburger
June 20, 2024
Sylvie Rest
June 20, 2024
The degree of automation in the German industry is steadily increasing. Worldwide, Germany is in...
Benjamin Kreuz
August 10, 2023